Best Practice Modelling Guidance at Various Project Stages
By Nishesh Jain, Research Fellow, University College London and DesignBuilder SoftwareThis article reviews the role that energy and environmental performance modelling plays at various stages of a building project, from initial planning, through design development to operation and post-occupancy. It explains key aspects of good practice modelling and points to industry resources (including DesignBuilder webinars and case studies) that provide structured modelling guidance at various design stages.
Introduction
The building procurement process goes through multiple phases, which cover activities from initial planning to post-construction handover and even the initial years of occupancy. The various project stages, as defined by RIBA, can be broadly categorised into four key procurement phases. These include project conceptualisation and planning, design development, construction and handover, and post-completion operations and maintenance (Figure 1).
Figure 1: Key building procurement stages mapped to project stages as per the Royal Institute of British Architects (RIBA).
As the building and project evolve, the activities related to performance modelling change.
During the initial planning stages, energy and environmental performance modelling is typically used to determine if the project targets and benchmarks can be achieved, thus enabling the project team to set realistic expectations. Besides this, at the planning stage, compliance-related modelling will also be carried out, if required, for local authority approvals (this process may extend into the design stage as well).
Modelling is typically undertaken during the project design stages (as shown in Figure 1). This modelling is often called ‘performance modelling’. The models created during design stages evolve as the design evolves and, over time, are customised to the project-specific details as they get finalised in the iterative design development process.
Further into the construction and handover stages, value engineering often drives design and specification changes. Therefore, on handover, the model should be updated so it aligns with the as-built building. Ideally, at this stage, the model should show that the intended operational energy and comfort targets are easily achievable.
The role of modelling does not necessarily stop once the building is occupied. Calibrated models can be used to help understand any underlying performance issues and provide insights into the operational inefficiencies, thus ascertaining their root causes. This is especially useful during the initial years of operation when the building and its system are finetuned.
Figure 2 summarises the typical modelling carried out during the key building procurement phases, along with various guidance documents and resources. Planning stage modelling for compliance and benchmarking varies by country and by region. Specific guidance on creating compliance models and local benchmarks is often provided by local regulatory bodies or industry organisations. In contrast, more broadly applicable guidance exists for performance modelling at the design stage and for post-occupancy evaluations.
The remainder of this article points to the resources available for these typical modelling tasks, covering both general guidance and DesignBuilder-specific learning.
Figure 2: Modelling tasks and documents at key building stages
Modelling at the Design Stage
Guidance documents and workflows
Performance modelling at design stages is undertaken to project the operational performance of a building and to facilitate design optimisation studies to improve performance. A robust modelling workflow must be followed to achieve the most accurate estimates and informed design decisions. Various performance modelling guides are available, including ASHRAE Standard 209, NABERS Design for Performance Guide and CIBSE TM54 (Figure 3).
Figure 3: Good practice performance modelling guidance documents
These guides explain the importance of accurately estimating modelling assumptions such as the operating hours and likely occupancy levels. They emphasise the importance of accounting for unregulated end uses such as lifts, escalators, small power loads, catering and server rooms in the building energy totals. The practical recommendations for good modelling emphasised in these guides can be broadly categorised into two parts:
- Better calculations: This involves the use of appropriate simulation software and project-specific assumptions.
- Improved presentation and explanation of results: A thorough comprehension among stakeholders can be achieved through scenario and sensitivity analyses and by comparing the performance against similar buildings—commonly known as benchmarking.
Our Design Stage Performance Modelling webinar covers the process of accurately evaluating operational energy use at the design stage following good practice modelling guidance. It uses CIBSE TM54 as an example guidance protocol, which is similar to the other modelling guides used globally.
Best practice design stage modelling process
The key steps in the performance modelling process include (Figure 4): creation of building geometry; assumptions for its occupancy, operations, and gains; implementation of HVAC system and its controls; and result analysis in a non-deterministic way, by assessing models’ sensitivity under different scenarios.
Figure 4: Various parts of modelling workflow
Geometry and Location: The accuracy and quality of model geometry are fundamental for all subsequent calculations and model outputs. Acquiring the best available climate data for a project is a common starting point as it can be used to inform design decisions even before modelling starts through a basic climate study. Apart from climate, many factors should be considered when generating a model, including keeping it simple and defining opaque and glazing fabric properties correctly. Details like thermal bridging and window frame effects should be considered and correct shading such as louvres, overhangs, canopies, other buildings and trees should be modelled. Another major aspect is to correctly configure zones and zone groups.
The model can be simplified for aspects that will have little to no effect on the model outputs, thereby saving valuable model setup and simulation time. Guidance on constructing a suitable model is available in the various guides, shown in Figure 3, in the following sections:
- ASHRAE Standard 209: Section 6
- NABERS Design for Performance Guide: Section 4.7
- CIBSE TM54: Section 7.2
- CIBSE AM11: Section 2.5
An important aspect of modelling is how to work with large models. DesignBuilder has been used to successfully model and simulate very large buildings with over 2000 zones and huge floor areas. DesignBuilder’s Knowledgebase article on Working with Large Models and Speeding up Simulations provides some useful tips on how to maximise productivity in cases of large models.
Occupancy, Gains and Operations: For an accurate model, correct activities and internal gains must be defined. Data on operation hours, occupancy levels, and loads and schedules for lighting equipment and other systems is required. These inputs are often based on assumptions and must be bespoke for each project. Data from typical industry standards such as ASHRAE or CIBSE can be used as a starting point, but for more detailed modelling, project-specific representative values should be discussed and agreed by the project team. A structured discussion with the client is useful for understanding typical patterns and the way that the building will be managed.
An introduction to setting up model data in DesignBuilder is available in our free tutorials, and a more comprehensive overview of setting up models for simulation can be found in our On-Demand Online Training.
HVAC Modelling and Simulation Results: Defining HVAC systems for space conditioning and ventilation is an important aspect of performance modelling as these systems are often the most intensive energy consumers. HVAC system modelling can be broadly divided into two categories (Figure 5):
- Simple HVAC – Loads and CoP-based energy calculations.
- Detailed HVAC – Component level modelling with performance curves.
Depending on the design stage, and the complexity of building systems and their controls, Simple or Detailed HVAC modelling can be used.
Typically, in early design stages, Simple HVAC methods are sufficient and HVAC energy use is calculated from plant loads and seasonal CoP values. However, at more advanced stages or where complex system controls are being modelled, component-level modelling using performance curves for HVAC energy calculations may be preferred. The level of detail in the HVAC model typically increases as the design evolves and more details on the system become available.
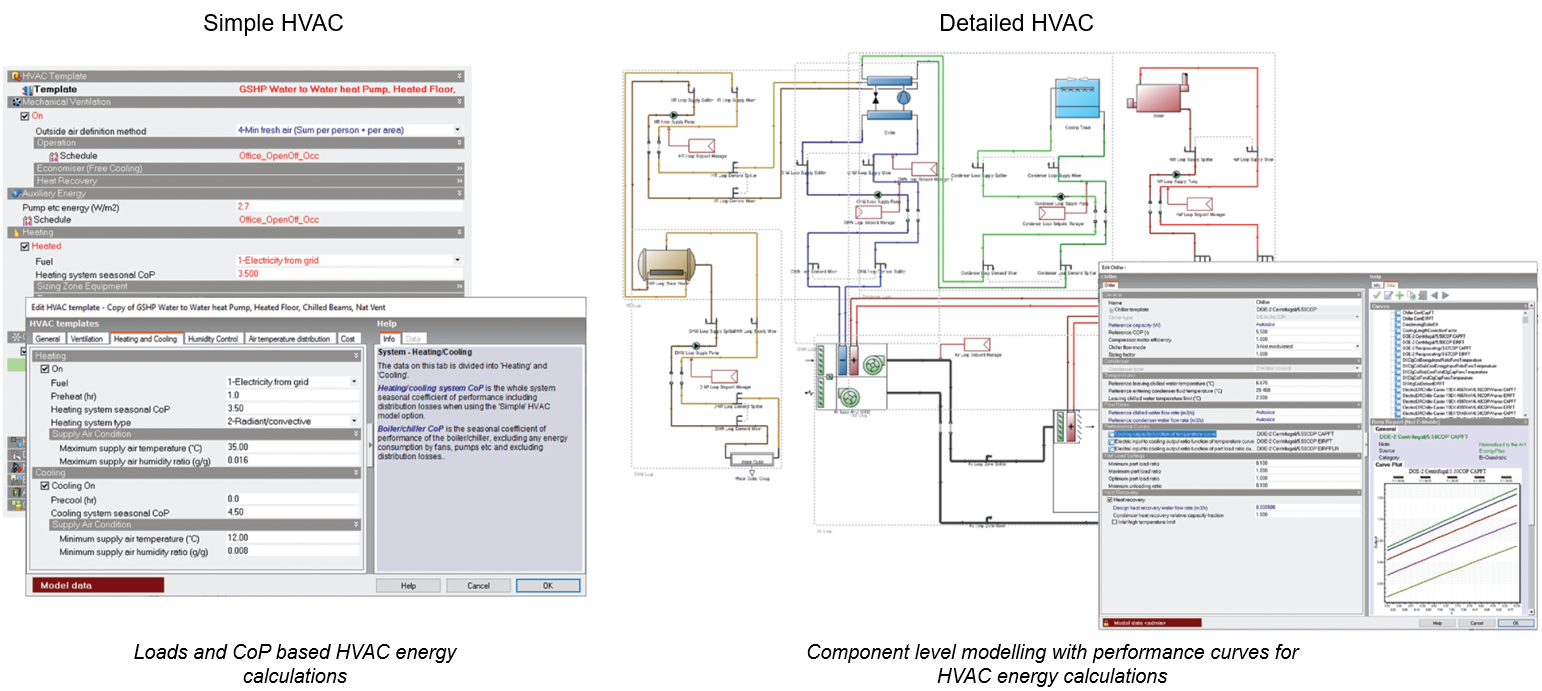
At early stages, simulations can be used to test and refine operational energy targets under a range of real-world scenarios using initial performance models and Simple HVAC. As the design progresses, it may be appropriate to introduce Detailed HVAC modelling. Besides performance fine tuning of HVAC system components such as heating and cooling plants, air-side equipment, heat recovery, fans, and pumps, Detailed HVAC can also be used for testing control options.
Our Modelling HVAC Systems - From Concept Through Detailed Design webinar shows a typical workflow from Simple through Detailed HVAC modelling to illustrate how DesignBuilder’s HVAC modelling options cater for all project stages and system complexities.
Once modelling is complete simulations can be run to assess the building performance. The tutorial Analysing results in DesignBuilder’s interface shows how to select and view a variety of simulation outputs.
Sensitivity and Scenario Analysis: In addition to the standard results assessment, the presentation of results should also account for model uncertainty. After the initial baseline projection, sensitivity analysis and scenario testing should be carried out at appropriate stages to understand the factors likely to have the greatest impact on the building’s energy consumption. This is done by presenting the results as a range of probable results.
To undertake sensitivity and scenario analysis, it is necessary to define the key parameters that might vary between the design and operation stage, such as HVAC system specs, operations protocols, occupancy patterns, etc. This operational data is normally collected through interviews with the stakeholders.
A structured way of assessing sensitivity is to conduct a multi-parameter analysis. This holistic analysis allows the combined effect of changing multiple inputs on the results to be determined. The combined effect may not be directly equivalent to the sum of its parts as some variables may cross-compensate for each other. DesignBuilder facilitates these analyses in an automated manner, and the functionality is fully integrated into the modelling interface (Figure 6). You can identify and rank design inputs in terms of importance. This parametric approach is especially useful in quantifying risk in projects procured under performance contracting, where more accuracy is required.
Figure 6: DesignBuilder Uncertainty and Sensitivity Analysis example
Our Uncertainty and Sensitivity Analysis webinar shows a detailed demonstration of the quantified risk assessment reporting process. The webinar explains how Sensitivity Analysis is used to measure and manage the risks associated with achieving state of the art “A” rating performance targets in an energy performance contracting project.
Modelling at Handover and Post Occupancy Stages
During construction stages, it is recommended that the simulation model is kept ‘live’ and updated with change decisions (e.g. ‘value engineering’). As a minimum, the model should be updated on practical completion, incorporating as-constructed commissioning information to ensure that, on handover, the model aligns fully with the actual building. This model can then be used to finetune the building during the initial years of occupation and indicate any remedial actions. Modelling, through the development of calibrated models, can be a vital tool to help in a robust building and systems evaluation during post-occupancy evaluation.
The use of calibrated models as part of post-occupancy evaluations and building retrofit projects has been detailed in various industry guidance documents including ASHRAE Guideline 14, IPMVP and CIBSE TM63 (Figure 7). These are complementary guidance documents. TM63 builds on Guideline 14 and IPMVP, especially in its use of model calibration as part of systematic post-occupancy performance evaluations.
Figure 7: Operational stage performance assessment guidance documents
TM63 provides a procedural and replicable evidence-based methodology for developing a calibrated model which can be used for diagnosing performance issues. This calibrated model sits at the heart of a step-by-step measurement and verification framework used to quantify and identify causes of building performance issues. In the case study, Using CIBSE TM54 and TM63 to Accurately Assess In-Use Performance in DesignBuilder, a design-stage performance model is calibrated in line with CIBSE TM63 for measurement and verification purposes.
Additional Resources
Other DesignBuilder resources to support your performance modelling include:
- Webinar: Advanced HVAC System Modelling
- Webinar: Design Optimisation: Making Rigorous Cost-Benefit Simulations a Reality
- Webinar: Uncertainty and Sensitivity Analysis: Simplify and Speed up Optimisation Studies
![]() |
About the Author Nishesh Jain, PhD, is a Research Fellow at the Institute for Environmental Design and Engineering (IEDE), University College London (UCL). He has worked as a researcher and practitioner in the field of energy modelling and operational performance of buildings. In collaboration with DesignBuilder Software, his current work focuses on developing new tools for operational performance assessments. He is a qualified architect, and for many years has been involved in performance simulation-related consultancy and research. Contact: n.jain@ucl.ac.uk |