Case Studies
These case studies highlight diverse modelling applications using DesignBuilder. Showcase your work and expertise to a global audience by featuring your project here. Contact us to get started.
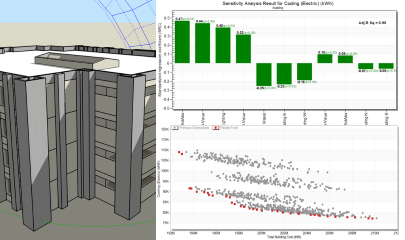
These case studies highlight diverse modelling applications using DesignBuilder. Showcase your work and expertise to a global audience by featuring your project here. Contact us to get started.