Case Studies > UK Certification
Design for Performance Assessment of an Office Refurbishment Project in London
About | Design for Performance (DfP) simulation modelling of a proposed office refurbishment | ![]() |
By | CHBS, for Kier Property | |
Location | 19-22 The Quadrant in Richmond, London | |
Category | Energy Modelling, Certification, Design for Performance | |
Highlights |
|
Introduction
This case study describes the operational energy modelling undertaken for a Design for Performance (DfP) assessment for a proposed office refurbishment project in London. The modelling was completed by CHBS, for Kier Property, the investment & development division of Kier Group, a leading UK construction and infrastructure services company. The project targeted high ratings for both Operational Energy DfP and BREEAM certifications using DesignBuilder Software. The project included modelling for The London Plan, Local Authority and Building Regulation compliance checks, proposing energy conservation measures to improve building performance, and modelling of operational energy and occupant comfort in accordance with CIBSE AM11 to fulfil DfP and BREEAM requirements.
The focus of this case study is to present the DfP modelling undertaken by CHBS, highlighting the unique aspects of DfP, Detailed HVAC modelling and ‘Off-Axis’ scenario studies
Overview of Design for Performance (DfP) Modelling
DfP modelling helps to ensure that the energy consumption of the project delivers against the design intent, overcoming the all-too-common performance gap between design and operation. It involves running detailed energy simulations to inform and test the design against a range of expected operating conditions to provide confidence that the performance target can be met. The building’s energy calculations in DfP includes the whole building’s HVAC system and all energy used in the common parts including lights, small power, lifts, external lighting, dedicated car parks, standby generator, etc
Base Build Model and HVAC System Modelling Details
The base case model for this building used appropriate area calculations for the rated area, representative constructions, and zoning to factor load distribution variations as per performance rating requirements. Figure 1 shows the DesignBuilder model used in the DfP modelling.
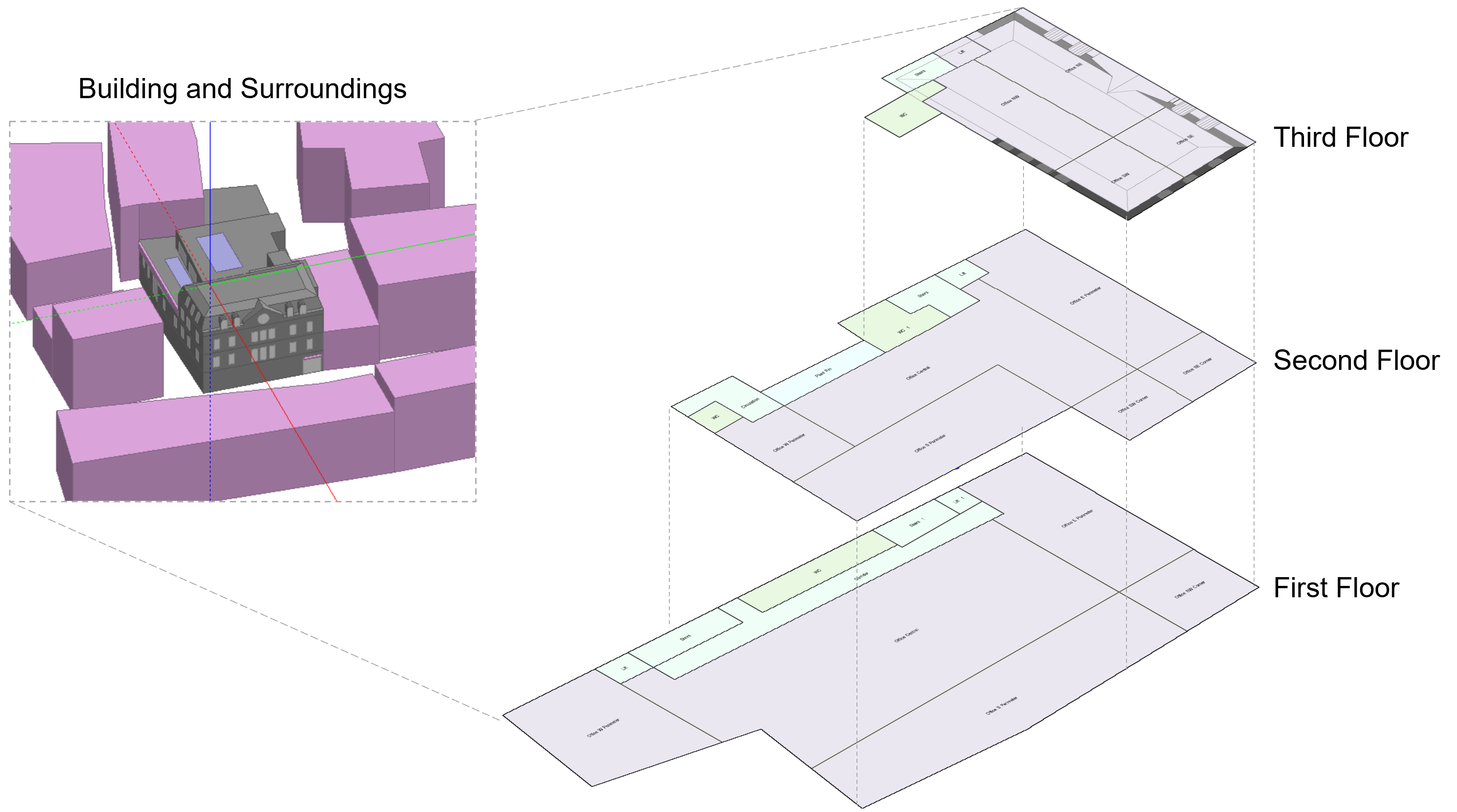
Figure 1: DesignBuilder Model used in DfP modelling
DfP requires modellers to have a sound knowledge of appropriate performance modelling tools to ensure the building and its systems are accurately modelled. DesignBuilder’s Detailed HVAC was used to simulate the energy use of the following systems:
- Variable Refrigerant Flow (VRF) systems were modelled to provide heating and cooling in the office areas, rear reception area and ground floor meeting rooms. The VRF systems were modelled using data available from the manufacturer. Where data could not be sourced certain assumptions such as library performance curves available in DesignBuilder (derived from Mitsubishi equipment) were applied.
- Localised MVHR units were modelled to provide the office areas, rear reception area and ground floor meeting rooms with fresh air. These units have been modelled as individual constant air volume air handling units with heat recovery.
- Space heating in circulation areas, WCs, and the shower/changing room on the ground floor of the building was provided with electric panel heaters.
- Individual exhaust fans were modelled in the WCs and Shower/Changing areas and the energy from these systems is included within the HVAC fans end-use category.
- Domestic hot water was provided to the building via a Mitsubishi PUHZ-SWVHAR5BS Air Source Heat Pump and a 300-litre hot water storage cylinder based on the manufacturer’s data.
Common area lighting and power use including lifts and external lighting loads were also defined as required. In addition, a Solar PV array with a capacity of approximately 14 kWp was included in the model.
At this design stage, as the operation and occupancy schedules for the building were unknown, default schedules were used in accordance with the guidance from the “Defaults for Simulations” of the Guide to Design for Performance.
Base Case Results and Risk Assessment
The reverse calculator was used to determine the maximum energy the building can use to achieve a desired performance rating. Figure 2 shows the Energy Use Intensity (EUI) that the building needs to achieve to obtain the various star ratings. To achieve a 5 Star rating the building EUI should be less than 70 kWh/m2.
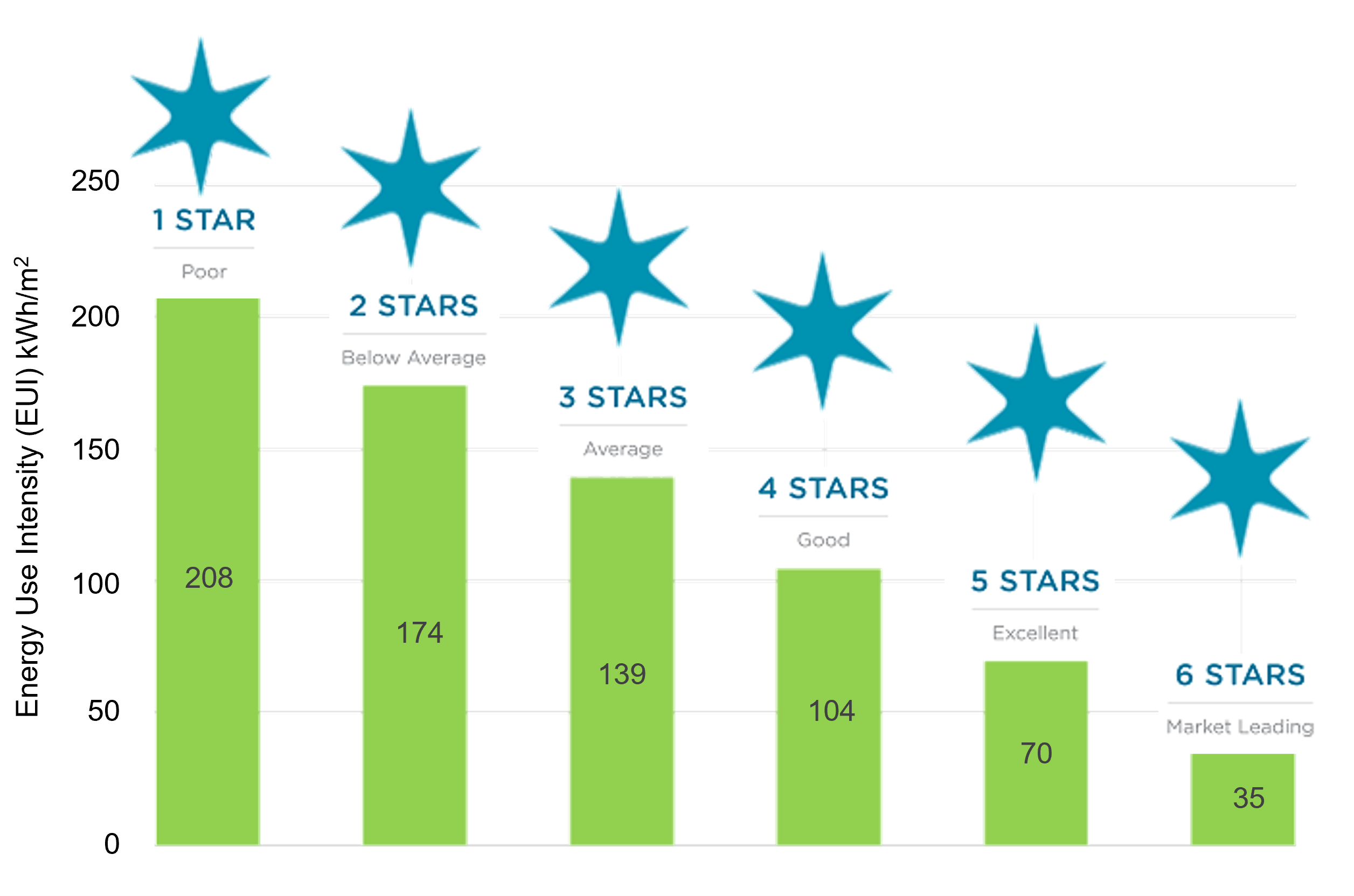
The base case scenario calculations show that with typical performance assumptions, the building will achieve an EUI of 62.69 kWh/m2. This indicates that the building has the potential to achieve 5.19 stars.
When conducting a design stage assessment, it was deemed necessary to consider several ‘Off-Axis’ scenario studies to assess risk. In accordance with the DfP guide, the base case model should be varied to explore risks to the building’s performance if certain changes related to building operations occur. These are termed as off-axis scenarios. In this case, four off-axis scenarios were assessed:
- Increased air permeability: This scenario assumes the target air-permeability figure in the base-case model has not been achieved due to lack of quality control from the contractor during construction. A ‘fall-back’ Air permeability figure of 5 m3/hr/m2 has been assumed.
- Adjusted Set-points: The tenants may require temperature set-points that differ from those used in the base-case model. This scenario assumes the set-points are changed to a tighter control band of 20ºC to 24ºC.
- Increased HVAC run hours: This scenario extends the operational hours of the HVAC equipment to 7am-7pm on weekdays and 9am-12pm on weekends.
- Increased Tenant small power: The tenants may exceed the small power figures that have been assumed in the base-case model. This scenario uses a tenant equipment power of 12.5 W/m2.
In addition to these scenarios, a combined risk scenario, which accounted for all above scenarios at the same time was also modelled. Results for the off-axis scenarios showed that there will be slight increase in the building’s projected EUI due to these changes. The combined off-axis scenario indicates that the overall impact of these potential risks would result in the building’s EUI increasing to 69.22 kWh/m2, reducing the potential rating to 5.01 stars (Figure 3).
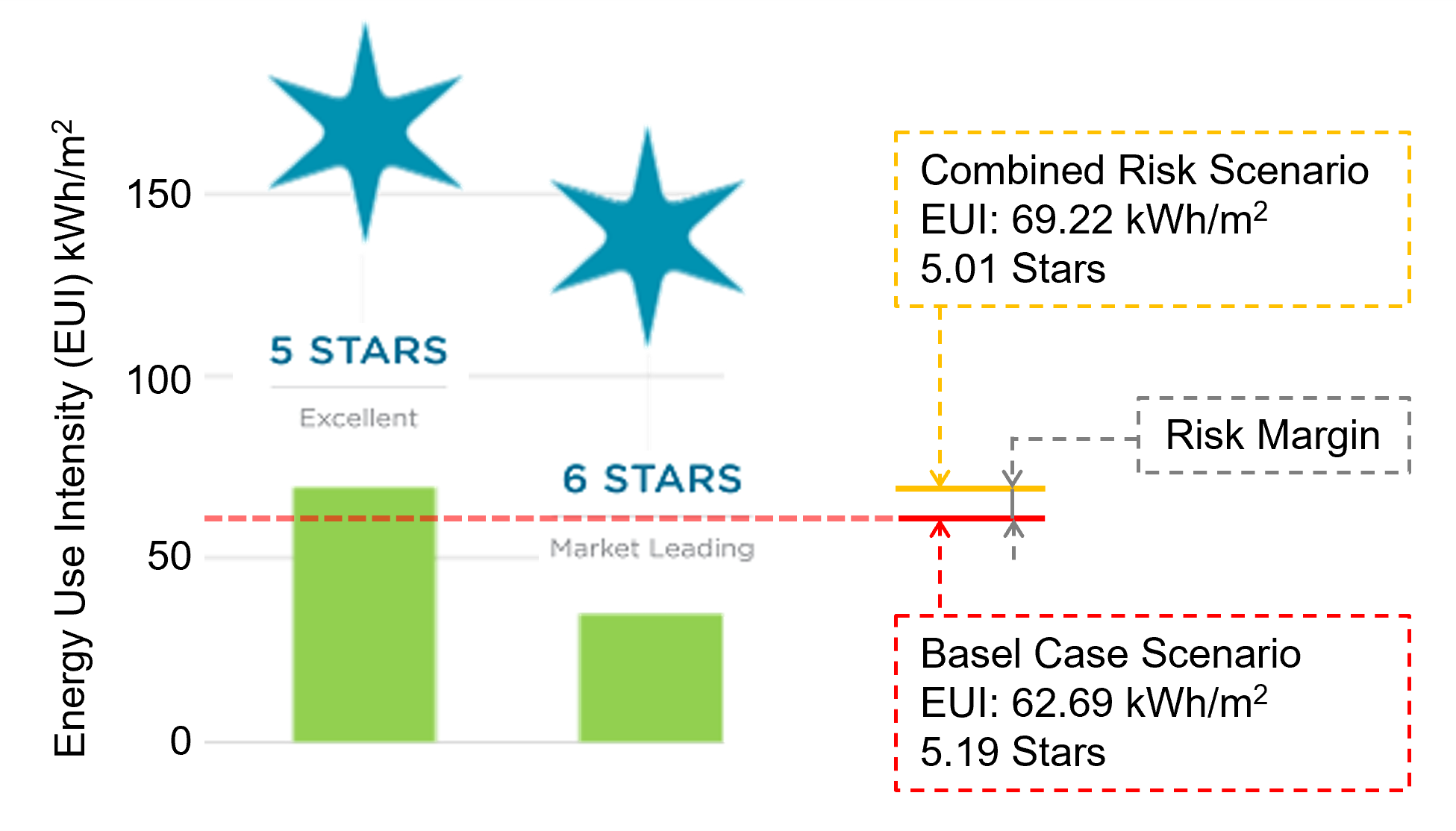
Conclusion
The current building design is highly energy-efficient, and it is likely to achieve a 5 star rating. In light of this the client is inclined to aim for operational net zero by further minimizing EUI to less than 55 kWh/m2 GIA/year or 70 kWh/m2 NLA/year and using electricity from renewable sources as the only fuel. Further measures that can help to meet the Operational Net Zero requirements are:
- Improving air tightness
- Improving insulation to existing external walls and roof
- Replacing or enhancing the performance of the existing windows
- Maximizing efficacy of internal lighting
- Maximizing installed solar PV capacity on the third-floor terrace and main roof
- Green Tariff electricity from green energy suppliers.
![]() |
About the Author CHBS offer a comprehensive range of sustainability, net zero & building services consultancy services to the UK property and construction industries. They have significant experience and expertise with an in-house team including Mechanical & Electrical Building Services Engineers, Licensed BREEAM Assessors & Advisory Professionals, Commercial and Domestic Energy Assessors and Whole Life Carbon Consultants. Website: www.chbs.co.uk |